
About our nonwoven products
The Functional Material Group provides a wide array of product lineup to suit clients’ needs.
We think out of the box to develop new materials that best suit your needs. It is enabled by our in-house
research center that is not common among our competitors.
WET-LAID NONWOVEN
History
Germany launched industrial production of nonwoven in 1920s, and in Japan it was in 1950s. Wet-laid nonwoven are adapted from Washi manufacturing technology, and Sansho engaged in development of the world's first wet-laid nonwoven paper made from 100% synthetic fiber.
Production
Fibers are dispersed into a water, form a sheet with papermaking screen, and wet-laid nonwoven is complete after drying process. It is very thin, also has high density and superior uniformity. In addition, we can make multifunctional non-woven by mixing various fibers.
Strengths
Manufacturing technology has been improving day by day, and the product quality is very stable. (ex, thickness, strength, permeability, filtration)
Fiber material
Vinylon, Polypropylene, Polyethylene, Polyethylene terephthalate, Acrylic, Rayon(viscose), Lyocell, Pulp.
DRY-LAID NONWOVEN
Production
The web forming process of dry-laid nonwoven does not use water, and it is bonded with heat, waterjet.
Strengths
Not only industrial application, but also food application is available by manufactured in clean room.
Fiber Material
Spunlace, Chemical bonding, Needle Punched, Thermalbonding Airlaid, Spunbond, Meltblown, Electrospinning.
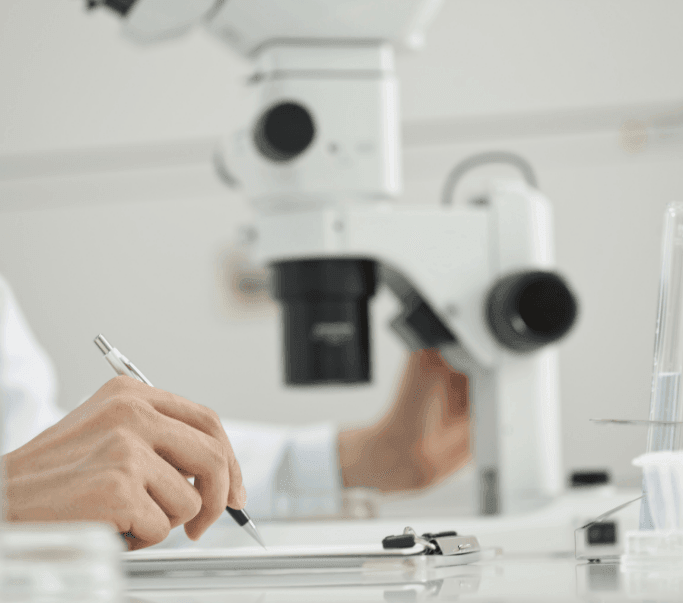
NON-WOVEN application technology
Laminate
01
Bonding nonwoven with film or plastic net provieds new function.
Density gradient
02
Laminating varous density nonwoven improves filtration performance.
Knead materials
03
Using fibers with kneaded functional agents can add new performance.